Unlocking the Possible of Light Weight Aluminum Casting: Proven Techniques for Success
Light weight aluminum spreading has actually long been acknowledged for its flexibility and widespread applications across various markets. Join us as we explore the vital components that can propel light weight aluminum spreading towards unmatched success in today's competitive market landscape.
Benefits of Aluminum Spreading
Aluminum casting uses a wide range of advantages that make it a preferred choice in various commercial applications. One of the primary benefits of aluminum spreading is its lightweight nature, which adds to sustain effectiveness in sectors such as automobile and aerospace. Furthermore, light weight aluminum is highly malleable, permitting complex and elaborate forms to be easily created via casting processes. This convenience in style is a considerable benefit for markets that require components with particular geometries.
In addition, aluminum spreading provides excellent deterioration resistance, making it ideal for applications where exposure to rough atmospheres is a problem. The product likewise shows excellent thermal conductivity, which is advantageous for markets calling for warm dissipation, such as electronics (about aluminum casting). Furthermore, light weight aluminum is completely recyclable, lining up with the growing focus on sustainable methods in modern-day manufacturing.
Design Factors To Consider for Casting
The layout stage plays an essential function in the total success of a light weight aluminum spreading task. One crucial consideration is the selection of ideal geometries and attributes that help with the casting process.
Furthermore, factors to consider associated with parting lines, gating systems, and risers are crucial to protect against problems like porosity and contraction. It is crucial to optimize the style for effective material usage and lessen post-processing needs. Simulations and prototyping can be useful tools in reviewing and refining the casting style prior to major manufacturing.
Partnership in between style producers, shops, and engineers is important to attend to any kind of prospective difficulties early in the design phase. By integrating these considerations into the casting layout process, suppliers can enhance item high quality, lower costs, and eventually open the complete capacity of aluminum spreading.
Enhancing Casting Effectiveness
When aiming to boost casting efficiency in aluminum casting jobs,Designing with a focus on maximizing material flow and minimizing issues is important. To achieve this, utilizing simulation software can aid in identifying possible issues prior to the spreading process begins. By simulating the circulation of molten aluminum, developers can change gating and riser styles to make sure appropriate dental filling and solidification, ultimately reducing the incident of problems such as porosity or shrinkage.
Furthermore, implementing appropriate warm treatment processes can boost the total spreading effectiveness. Warm therapy can assist improve the mechanical properties of the aluminum spreading, making sure that the final component meets the needed specifications. Furthermore, employing automation and robotics in the casting procedure can improve manufacturing, lower hands-on labor, and rise overall performance.
In addition, constant monitoring and quality assurance during the casting procedure are important for identifying any type of discrepancies and guaranteeing that the last products meet the desired criteria. By implementing these strategies, makers can boost casting efficiency, boost item high quality, and inevitably accomplish greater success in light weight aluminum spreading projects.
Quality Assurance in Aluminum Spreading
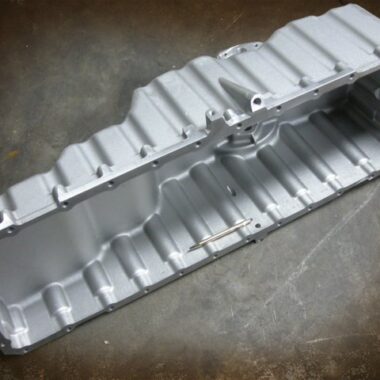
Effective top quality control practices play an essential duty in guaranteeing the accuracy and reliability of aluminum casting processes. Quality control steps in aluminum spreading encompass a range of activities intended at promoting specific criteria and recognizing inconsistencies that can endanger the last product.
In addition to process control, high quality control in light weight aluminum casting involves rigorous testing and assessment treatments at different phases of production. By carrying out durable top quality control practices, aluminum spreading facilities can supply items that satisfy customer expectations for top quality, performance, and integrity.
Maximizing Productivity
To accomplish optimal financial performance, an extensive approach for making best use of success within aluminum casting procedures have to be carefully devised and implemented. One vital facet of maximizing profitability in light weight aluminum casting is maximizing manufacturing efficiency.
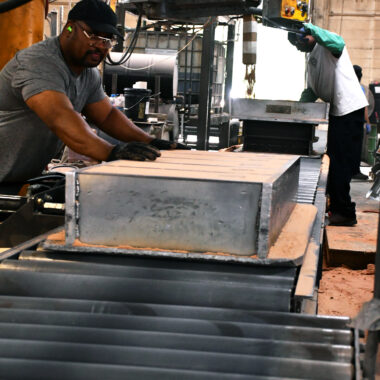
Additionally, expanding item offerings and checking out new markets can aid expand earnings streams. Recognizing customer demands and market patterns can lead calculated choices to maximize emerging chances. Purchasing study and development to innovate products or processes can also drive earnings through distinction and customer contentment.
Final Thought
To conclude, aluminum casting uses many advantages in regards to design flexibility, durability, and cost-effectiveness. By thoroughly considering layout considerations, improving casting effectiveness, executing top quality control steps, and making the most of success, manufacturers can open the full potential of aluminum spreading. This flexible and dependable procedure has shown to be a successful choice for a large range of commercial applications.
In addition, light weight aluminum is Related Site extremely flexible, enabling for intricate and complex shapes to be conveniently generated with spreading procedures.Reliable quality control techniques play an essential duty in guaranteeing the precision and reliability of aluminum casting procedures.In enhancement to procedure control, high quality control in light weight aluminum casting involves extensive testing and assessment treatments at various try these out stages of production. By carrying out robust top quality control methods, aluminum casting facilities can supply products that meet consumer expectations for high quality, performance, and reliability.
By very carefully considering style considerations, improving casting effectiveness, carrying out quality control steps, and taking full advantage of productivity, makers can open the full possibility of light weight aluminum casting.